EasyMining is Recycling Nutrients Agriculture Needs
How a 141-year-old waste management company is pioneering the recycling—rather than mining—of phosphorus and other nutrients we need to keep feeding the world.
UPPSALA, Sweden
he person who discovered phosphorus was hoping to find something else. In Hamburg in 1669, the self-styled chemist Hennig Brand was, like many of his peers at the time, trying to turn base metals into gold.
Believing that the human body was the key, he boiled large amounts of urine and heated the residue, eventually producing a white, waxy substance that glowed in the dark. Brand called his discovery phosphorus, from the Greek for “light-bearer.” (He later sold his supply for 200 thalers—about $13,300 in today’s money—when he needed some cash.)
For more than a century phosphorus was made through this method, for example to produce an early version of matches, until in the 18th century a couple of Swedish chemists discovered that calcium phosphate could be sourced from bones, which became an early fertilizer. This and other discoveries eventually led to the development of commercial fertilizers, by far the largest global use for phosphorus, and enabled the Green Revolution and a massive global population boom.
But the way we source phosphorus—mining it from reserves in a handful of countries and importing it—is unstable and unsustainable. Phosphorus feeds the world, but also pollutes it, and phosphorus prices and conflict are disrupting food production. There’s a race on once again to revolutionize how we get our phosphorus, and scientists are, as they were at the beginning, looking at human waste for answers.
In 2005, Yariv Cohen, then a 34-year-old chemical engineer, was working on this problem when he made his own accidental discovery. While conducting PhD research in recovering phosphorus from sewage sludge ash—a by- product of incinerating sewage sludge—at Sweden’s University of Agricultural Sciences, he set up an experiment to recover phosphorus in the form of a highly concentrated ammonium phosphate solution. “I was testing a new idea for concentrating the solution without water evaporation—by circulating the ion exchange regeneration solutions and adding ammonia in a particular way to obtain a final product with as high a concentration as possible,” he says. He then left it to run overnight.
“I came to the lab in the morning, and instead of finding a highly concentrated solution as I expected, the system was completely clogged with white crystals, like it was covered with snow,” says Cohen.
“Initially, I was disappointed that the experiment failed,” he says. But it hadn’t: the white stuff turned out to be pure ammonium phosphate crystals, and he realized he had indeed found a method to recover solid phosphorus crystals without the need for evaporation—a new, more energy-efficient way.
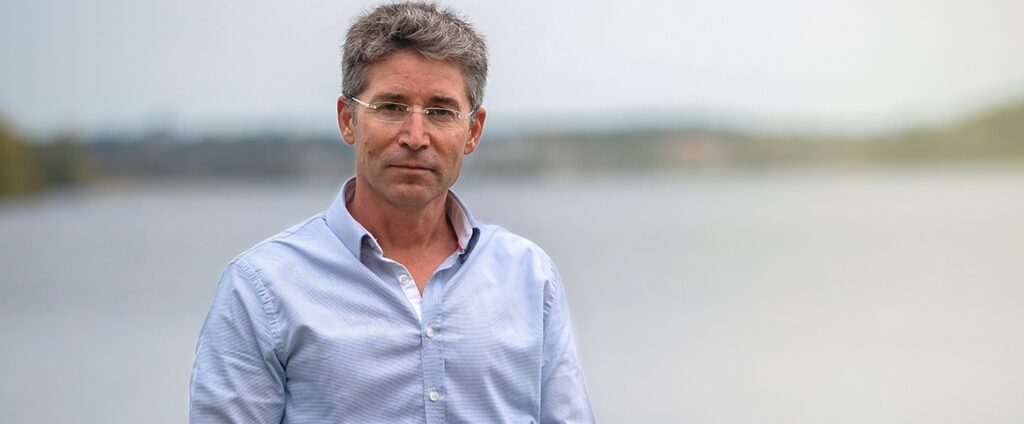
Cohen’s PhD research and years of investigating phosphorus recovery techniques led to his current role as head of research and development at Sweden’s EasyMining. The company now holds several global patents for the extraction and recovery of resources from wastewater, sewage, and fly ash—a byproduct of incinerated waste—for which the company, along with its parent, Ragn-Sells, is shortlisted for the 2022 Food Planet Prize. Their technologies can potentially improve food security by recovering nutrients—producing better quality than mined ones—from waste to reuse in fertilizer and other uses, instead of relying on unstable global supply chains.
“The whole value chain needs to be changed,” says Cohen. There are many ways to recover nutrients from our food and waste cycle, but it’s not being done at a large scale—yet. “Quantities matter and quality matters,” says Cohen, when it comes to making recovery viable. Both are a challenge.
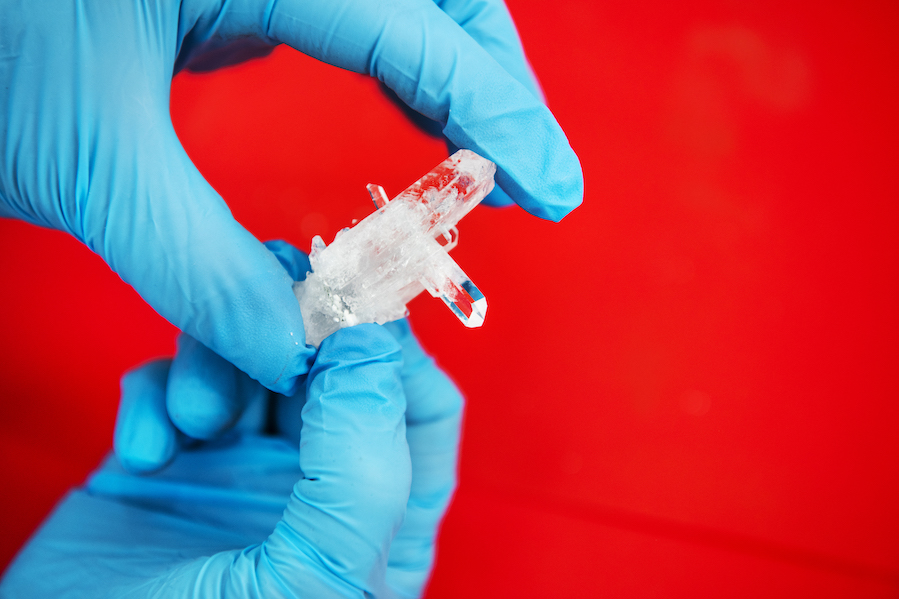
Put simply, there is no life without phosphorus. Phosphates are essential for bones and teeth, for DNA, and for every living cell. As an essential ingredient in all fertilizers, it’s also crucial for crop growth. “Plants need all three—nitrogen, phosphorus, and potassium—to grow,” says Cohen. But unlike nitrogen, phosphorus is finite: it cannot be replaced, substituted, or manufactured.
The world’s phosphorus supplies—which took millions of years to form— are depleting, with reserves of phosphate rock concentrated in a handful of countries. Morocco, China, Egypt, Algeria, and Syria control 85% of the world’s phosphate rock reserves. About 80% of mined phosphate rock—sedimentary rock containing fossilized deposits composed of remains of animals, algae, and sea creatures—is converted into mineral fertilizers for global food production.
As earth’s population grows, we will need more phosphorus to produce food at a time when it’s becoming more scarce and much more expensive. The biggest need is in developing countries, which are already affected by rising prices. One large study released this summer states that global phosphate prices have risen 400% since 2020 and 1 in 7 farmers can’t access or afford phosphorus.
The largest share of the world’s phosphorus reserves—around 70%, according to the latest US Geological Survey—is located in Morocco and the Western Sahara. China’s 5% of phosphorus reserves is a distant second, but China is the world’s largest producer, and if it keeps producing at the current rate, its reserves will be depleted in the next 35 years. There is only one operating phosphorus mine in the European Union, in Finland. This mine produces 1 million tonnes annually, about 10 percent of the EU’s need, and is projected to be depleted by 2035.
Along with having the most reserves, Morocco is the world’s largest exporter and the second largest producer of phosphates, if one includes Western Sahara, a long disputed territory where the remote Bou Craa mine is located. This mine has one of the world’s largest phosphorus deposits, at 1.7 billion tons, and currently produces 3 million tons annually. The mined rock is transported on the world’s largest conveyor belt system from the mine to the coast 61 miles away, from where it is shipped all around the world.
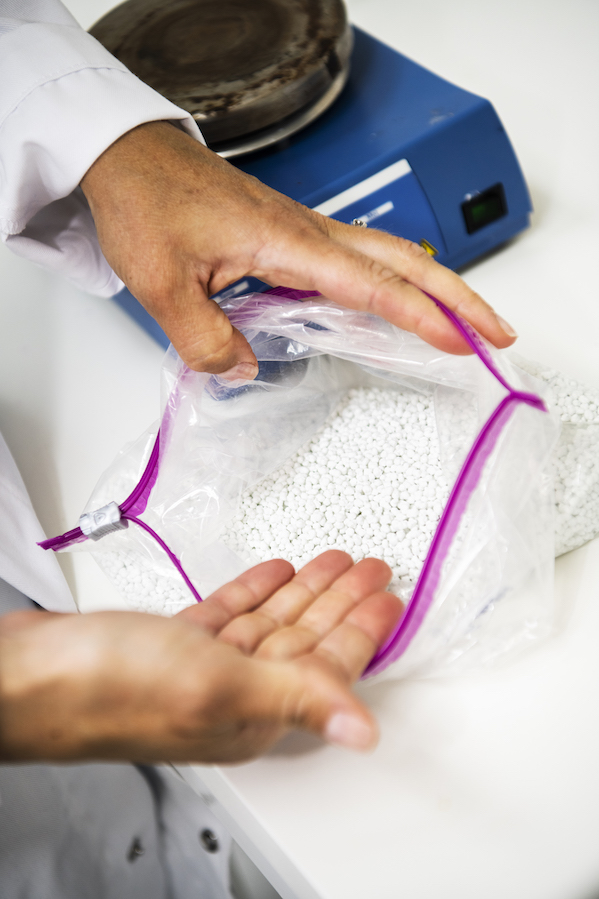
“Most of us, most days, will eat some food grown on fields fertilized by phosphate rock from [Bou Craa] mine,” environmental author and journalist Fred Pearce noted in Yale’s University’s Environment360 blog. Conflict and high costs have already disrupted production in Morocco. Unless we can recycle more phosphorus or access other sources, Morocco’s share of worldwide production could be 80% by 2100, a level of concentration that is inherently dangerous to global supply chains.
There is now another pressing problem with phosphorus and food security on the European continent. Russian-mined phosphate dominates the European import market, and the war in Ukraine was a looming topic at the 4th European Sustainable Phosphorus Conference (ESPC), held in Vienna in June 2022.
“Currently, the phosphorus price is so high because of a shortage we already had, and [Ukraine’s invasion by] Russia,” says Ludwig Hermann, President of the European Sustainable Phosphorus Platform, which organized the conference.
Mining is precarious, but phosphorus needs are rising. That is why phosphorus recovery, long discussed but little implemented (at least not at scale), is having its moment. Phosphorus mines may be finite, but the substance can be recovered in several different ways from sources such as human waste, plant matter, manure, and the waste of food that has been treated with phosphorus fertilizer.
In 2019, over 500 scientists signed ‘The Helsinki Declaration,’ calling for food, agriculture, waste and other sectors to improve global phosphorus sustainability.
At the ESPC in Vienna, over 300 people gathered at the Andaz Hotel conference center to discuss the latest in phosphorus sustainability—from across science and academia, industry, energy companies, fertilizer companies, researchers, journalists, politicians, EU policymakers. At the hotel’s conference center, attendees mingled around standing tables with coffee and Viennese pastries, but also among jars containing samples of fertilizer pellets, sewage sludge ash (which resembles ground coffee) and calcium phosphate (a white powder) that had been recycled, rather than mined.
Their goal: to arrive at what Christian Kabbe, CEO of EasyMining’s Germany office, calls the “reality stage.” That means not just recovering phosphorus, in large enough amounts and good enough quality—scrubbed of a lot of the toxic heavy metals such as cadmium and uranium that exist in sewage sludge ash— but also finding the market for it.
“Recovery tends to still be technology focused, and few have explored the market side,” says Kabbe. The amount of recovered phosphorus is also crucial: “There must be volume for recovered phosphorus to be viable. It can’t be pocket dust.”
Cohen’s lab “accident” as a PhD student resulted in EasyMining’s first patent, for Clean-MAP, a method for extracting ammonium phosphate from mining industry waste. Cohen and his colleague, Patrik Enfält—plus one investor— founded EasyMining in 2007 to commercialize its technologies. Since then, EasyMining has produced several patents, with the help of investment and support from its much older parent company.
Ragn-Sells is Sweden’s biggest waste management, recycling, and environ- mental services company. The three-generation family business has a waste management pedigree dating back to 1881, when Amandus Zakarias Leonard Sellberg set up a haulage company—at first, with just one horse—transporting latrines from central Stockholm to farms in the countryside. In 1928, on his wife Julia’s family farm, Amandus and Julia’s son, Ragnar Sellberg, started a waste collection service for local home-owners. In the 1960s, Sellberg steered the company’s activities into waste management and recycling.
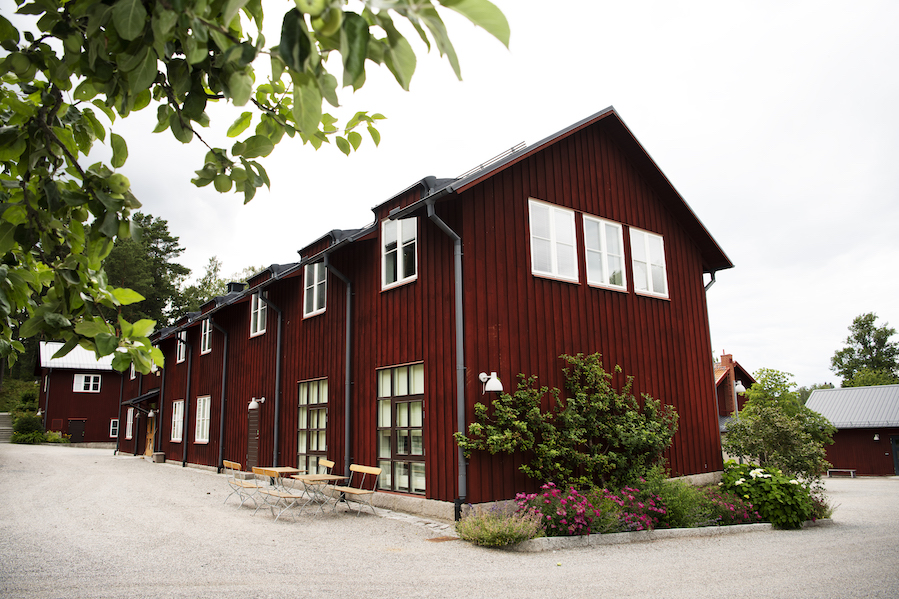
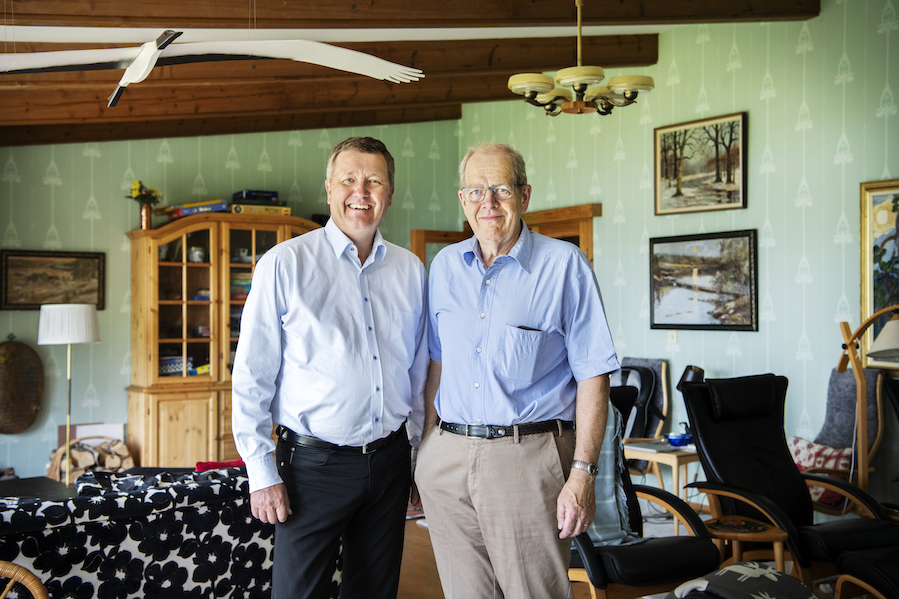
Ragn-Sells’ head office remains at the bucolic (but updated) Väderholmens Gård (farm) in Sollentuna, 11 miles north of Stockholm. On an early June afternoon, birdsong accompanies the hum of a robotic lawn mower ambling over manicured gardens in front of the company’s executive offices in an airy, sunny building. Electric car charging ports adorn the farm buildings—a cluster of wooden barns painted the “Falu red” pigment common in Scandinavia.
Ragnar’s son, Erik Sellberg, Chairman of Ragn-Sells, explains that he never intended to go into the family business: he was studying economics when he seriously injured his knee in a boating accident. In his convalescence he started working with the family firm, and in 1981 he joined Ragn-Sells full time. He invested in EasyMining in 2008, at first only privately, based on a “gut feeling,” In 2014, Ragn-Sells bought EasyMining outright. “I saw that what they do fit into our thinking of how to save resources,” says Sellberg.
“The long-term perspective of a family-owned company is what enables EasyMining to grow and develop,” says Cohen. Ragn-Sells, with its extensive experience in environmental management, is also willing to take the risks and challenges associated with producing new technology at large scale, he adds.
The acquisition of EasyMining, which now has 40 employees based between Uppsala, Gothenburg, and Berlin, aligns with Ragn-Sells’ long-held values. A banner in the office lobby displays a quote by Ragnar Sellberg: I see a beginning where others see an end. Ragn Sells’ and EasyMining’s mission is to help transform our linear economy—in which raw materials are collected, used, and dumped—to a circular economy in which we re-use and recirculate resources as much and for as long as possible. Our waste products contain valuable materials.
“Our strategy as a company is the belief that in the future, there will be no waste,” says Lars Lindén, Ragn-Sells’ CEO.
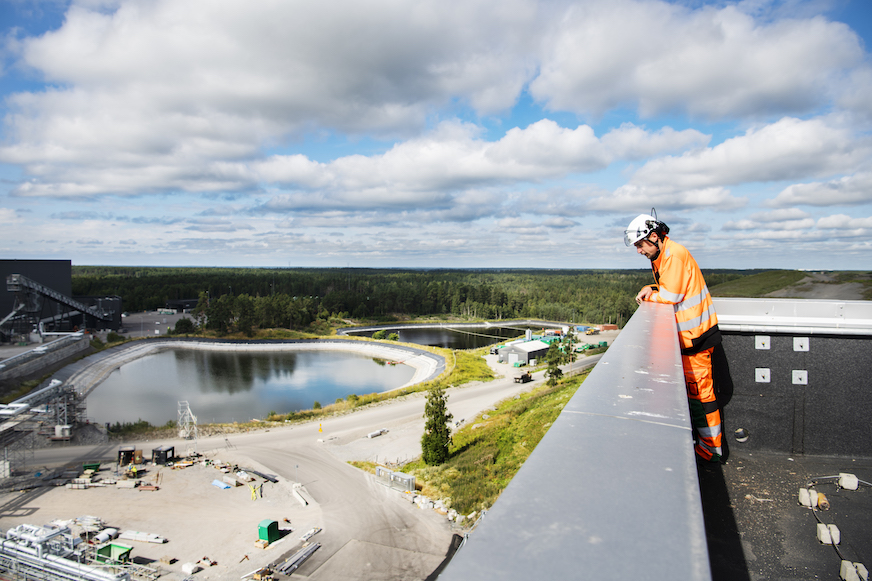
EasyMining’s roots are in phosphorus recovery, but it also holds patents for recovering other nutrients. Project Nitrogen (a working title) is currently being applied in partnership with BIOFOS—Denmark’s largest wastewater utility—to recover ammonium from wastewater at a demonstration plant in Copenhagen.
Ash2Salt recovers commercial salts from fly ash, which is produced from incinerating waste and usually exported or landfilled, neither of which are sustainable. The new Ash2Salt plant at Högbytorp, a few minutes from Väderholmen, will be fully operational in late 2022 through a licensed agreement with Swiss-Japanese energy-from-waste company Hitachi Zosen Nova. The plant will wash and treat fly ash at large scale to recover several types of commercial salts for de-icing roads and fertilizer, among other uses, and reduce dependence on mined salt.
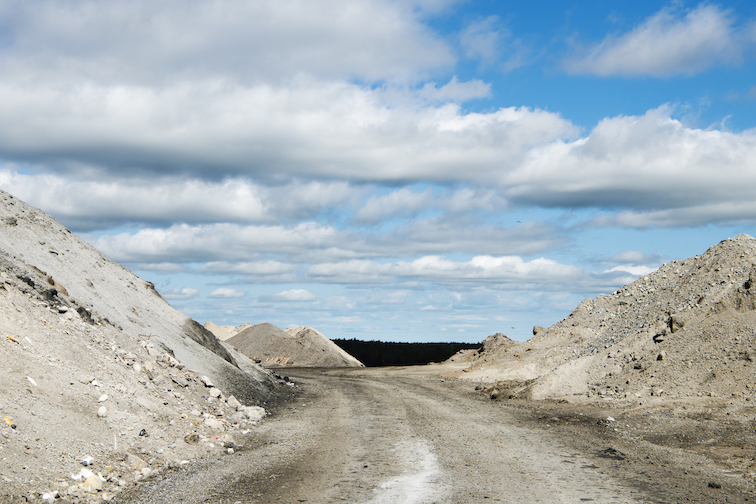
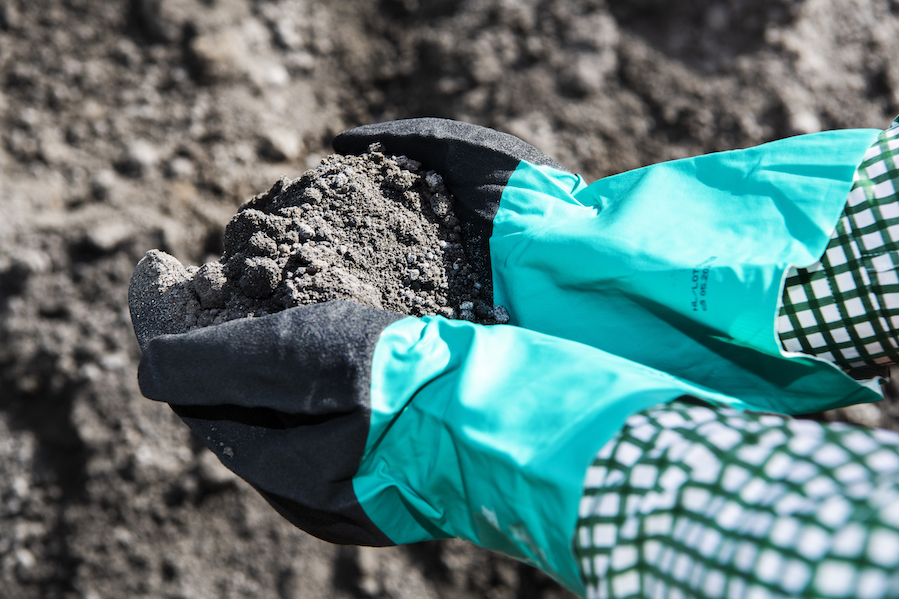
But perhaps the largest opportunity for recovering nutrients such as phosphorus, right now, is in wastewater. “We want wastewater treatment plants to be the resource plants of the future,” says Pär Larshans, Ragn-Sells’ Director of Sustainability.
Dealing with wastewater—of which sewage is a subset—has been a challenge for as long as humans have gathered in great numbers. In Europe and North America, municipal sanitation systems grew out of the need to reduce typhoid and cholera outbreaks during the Industrial Revolution. London’s Great Stink of 1858—when hot weather and untreated sewage flowing into the Thames resulted in a major cholera outbreak, and made the city smell so bad that Members of Parliament soaked their curtains in chloride of lime—led to the construction of an extensive underground sewage system to convey sewage away from the population.
In the 19th century some cities began treating sewage—by settling it in lagoons, adding oxygen to reduce odor, or adding chemicals—in an effort to reduce water-borne disease outbreaks—a development that led to a huge increase in life expectancy. Starting in the 1840s, some sewage started to be applied to agricultural land as a fertilizer, with some success.
Even today’s treated wastewater contains large amounts of nutrients such as phosphorus and nitrogen—passed from agriculture and fertilizers to food and to our own waste—which is a waste disposal challenge, because they contribute to water pollution and eutrophication, an overgrowth of algae that can turn water bodies toxic. Sewage sludge, a semi-solid byproduct of wastewater treatment, is rich in nutrients but also in pathogens, so it has to be treated before disposal or reuse for agriculture. In most cases it is incinerated, a process that started in the 1930s.
Today, “there are three reasons to incinerate sewage sludge,” explains Cohen. Incineration detoxifies the sludge of pathogens, it increases the concentration of phosphorus (there is 0.8% phosphorus in sewage sludge, but 9% phosphorus in sewage sludge ash, as compared to 1.8% in rock phosphate from Finland’s phosphorus mine), and it reduces weight and volume by 90 percent, making logistics and transport simpler.
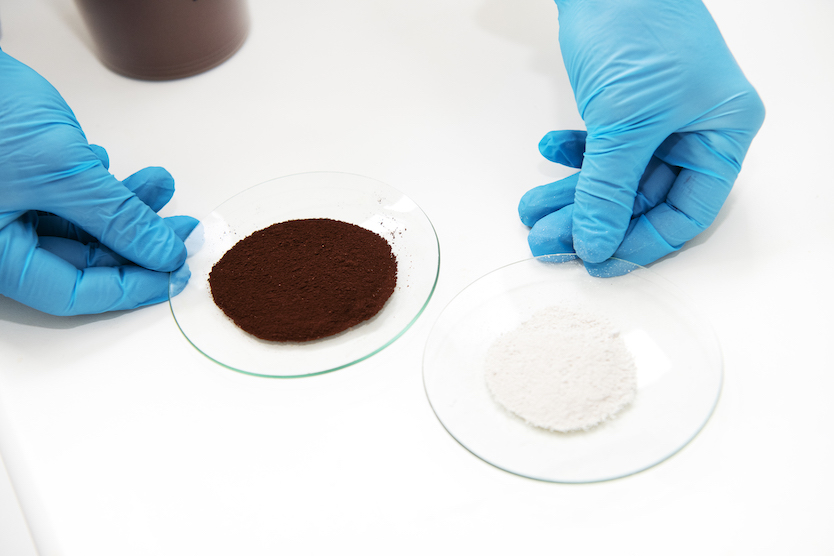
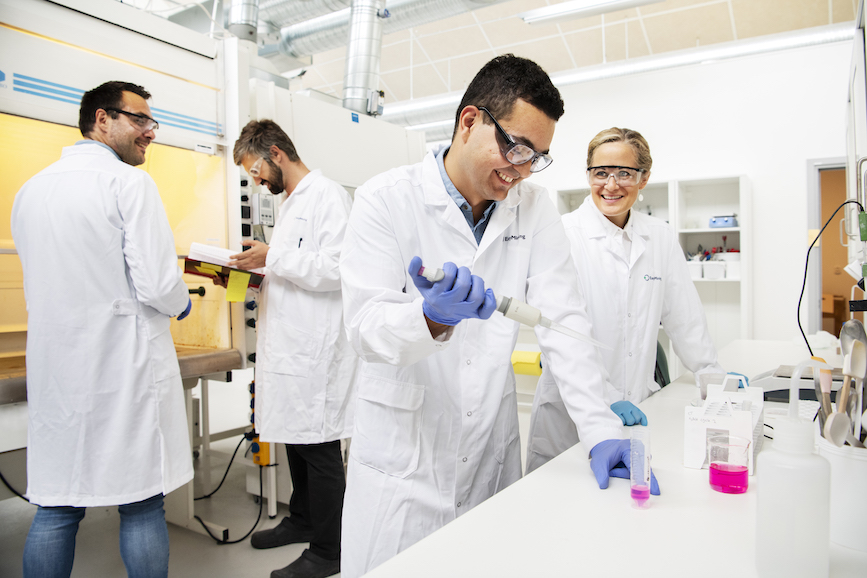
EasyMining’s Ash2Phos process—which involves treating sewage sludge ash with a series of chemical reactions employing hydrochloric acid, alkaline, and lime—can recover 90 percent of the phosphorus in sewage sludge ash, with a more than 96% reduction in contaminant heavy metals such as cadmium and uranium. The main substance it recovers is calcium phosphate—equivalent to mined rock phosphate, but with higher purity (mined Moroccan phosphate for instance is high in cadmium).
The process also has lower carbon dioxide emissions compared to sourcing virgin resources. A life-cycle assessment study by the IVL Swedish Environmental Research Institute concluded that producing the same amount of calcium phosphorus from ash with the Ash2Phos process compared to sourcing it from non-renewable phosphate ore would save 20,000 tons of carbon dioxide annually.
The first Ash2Phos plants—the first in the world that will recover phosphorus at this scale—are in development in Germany and Sweden. The German plant, in Schkopau, is a partnership with utilities company Gelsenwasser and is projected to be completed in 2024.
That’s the recovery side; regulations make the market side a greater challenge. There are three potential routes for the recovered phosphorus that EasyMining obtains: fertilizer, animal feed, and food additives. While the EU is facilitating a move to a circular economy, there remains a legal barrier to achieving this because current EU laws prioritize origin, rather than quality, of phosphorus and other recycled nutrients.
“EasyMining’s recycled phosphorus cannot be used for feed, no matter the quality, and cannot be used for food additives, no matter the quality, because of its origin,” says EasyMining’s Kabbe, in Vienna. This despite that the recycled phosphorus is of higher purity than that in traditional fertilizers.
Products recycled from waste can’t be used for agricultural feed for animals or for food additives. This legal taboo is a relic from the BSE (“mad cow disease”) crisis in the United Kingdom in the 1980s and 90s. Back then, however, there was no significant nutrient recycling from waste to be used. “When these laws were written, nobody was doing what we are doing yet,” says Anna Lundbom, EasyMining’s marketing manager.
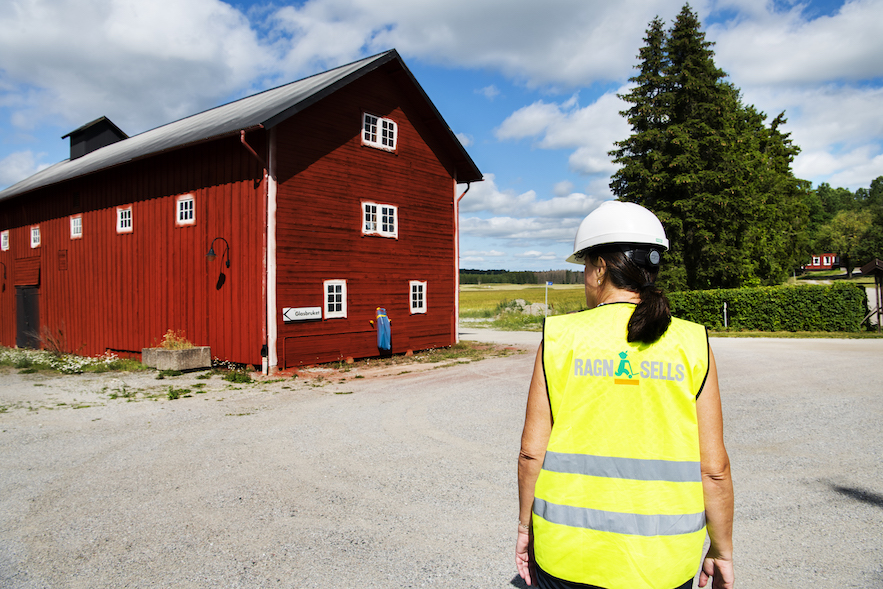
While there is a market for recycled nutrients for fertilizers in conventional farming, there is also still a ban on their use in organic farming. This would seem to deprive recovered phosphorus of a natural target market. What better evangelists and early adopters of a circular economy than organic farmers and their consumers?
The needle may be slowly moving on that front. The 2022 working program of the EU’s Expert Committee on Organic Farming includes the consideration of allowing some recycled nutrients in organic farming. Should the EU decide to open the directive, it will be possible to apply for an exemption from the law, explains Larshans, although ideally the law itself would change.
This change in attitude, says Larshans, could be “an important starting point for future sustainable farming.” With that shift, by 2025 EasyMining could be able to supply organic farmers with recycled organic fertilizers.
Ludwig Hermann of the European Sustainable Phosphorus Platform is a little more cautious in his optimism. “So far, nothing has happened, but some movement seems to be detectable,” he says.
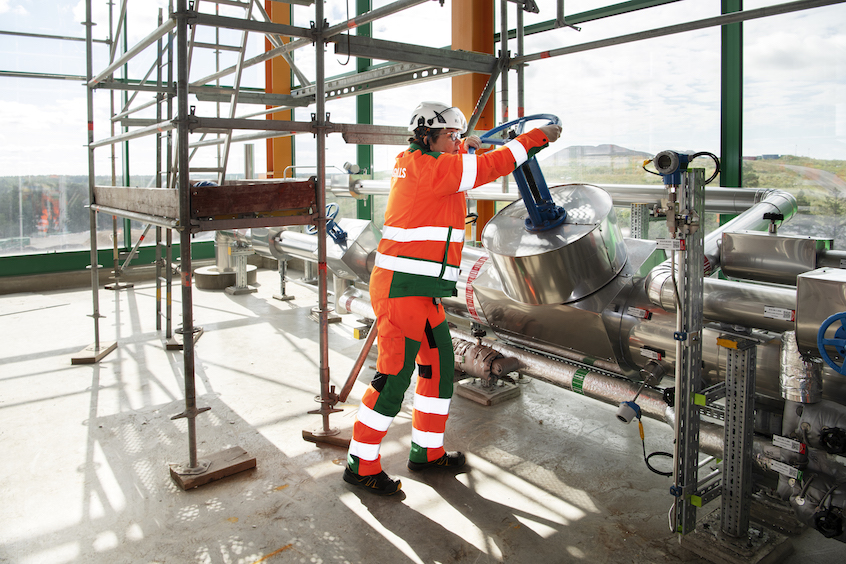
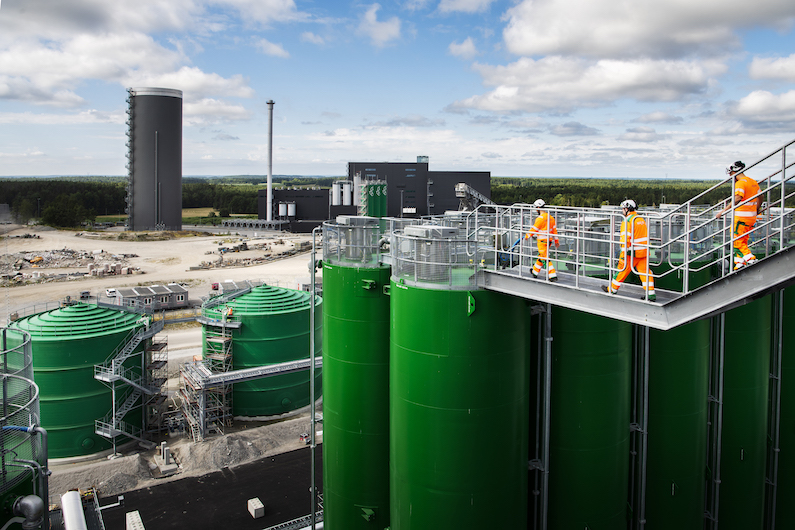
There are other challenges to the wider application of nutrient recovery technology. Hermann mentions two: cost and risk perception.
“There will be a cost increase, albeit small, for phosphorus recovery, and a debate about who pays, which will probably be citizens, probably through wastewater treatment,” says Hermann. “In Austria, we have an annual bill for wastewater treatment. From 300 euros a year, it might be 303 euros,” he says.
But politicians will be reluctant to impose costs, no matter how little, he points out, particularly with the current energy and inflation issues.
At present, there is also limited experience with large-scale phosphorus- recovery. “Because it is not yet widely available, there is an additional risk perception,” says Hermann. Still, his feeling is that EasyMining’s plants in Germany and Sweden will set the ball rolling in the rest of Europe, and elsewhere.
“It is quite challenging to set up large-scale production of new processes to move to a circular economy,” says Cohen. “In addition to the main recovered product, you need to develop and find offtakes for all by-products, and in contrast to the mining industry, any disposal of residues will require, in several countries, paying landfill tax.”
It’s difficult to compete with the traditional way of producing fertilizers, he adds. For example, OCP, Morocco’s largest phosphorus producer, simply discharges the waste into the sea at low cost.
Legislation for recovering phosphorus is creating a market—in Europe at least—for wider implementation. In 2006, Switzerland enacted a law to make
the recovery of phosphorus from slaughterhouse waste and sewage sludge obligatory. Germany—which has the most sewage sludge ash in Europe—has introduced a phosphorus recovery law stipulating that wastewater treatment plants above a certain capacity will have to recover phosphorus from sewage sludge by 2029, and have a plan for doing so in 2023.
Austria has been considering a law for phosphorus recovery, but it is not yet mandatory. Still, on June 19, 2022—the day before the city hosted the ESPC— Vienna’s City Hall announced its own plans to recover phosphorus from sewage sludge ash. The City of Vienna’s local authority and Wien Energie, Austria’s largest energy provider—which already incinerates wastewater and garbage for reuse at its surreal, Hundertwasser-designed Wonka’s Chocolate Factory of a plant in Vienna’s 9th district—plan to build and operate a plant to process sewage sludge ash by 2030.
Nicole Puzsar, head of public relations for Stadt Wien, or City of Vienna, says the first crude plans for recovering phosphorus in Vienna date back to 2015. “A well-functioning waste management economy has always been a high priority for Vienna, which also considers itself a pioneer in the field of the circular economy,” says Puzsar.
Above all, partnerships across fields and borders are necessary for moving towards nutrient recovery and to a circular economy. “Cooperation, knowledge, technology, and expertise-sharing is the key to making this work,” says Larshans. “Market demand is there, policies are on their way, but we need to speed up the process,” he adds.
EasyMining’s Kabbe describes it as a “push-pull” process between industry, innovation, and science, and getting regulators and policymakers on board. “The costs on the market level are competitive,” he says. “Now, it’s a political question.”
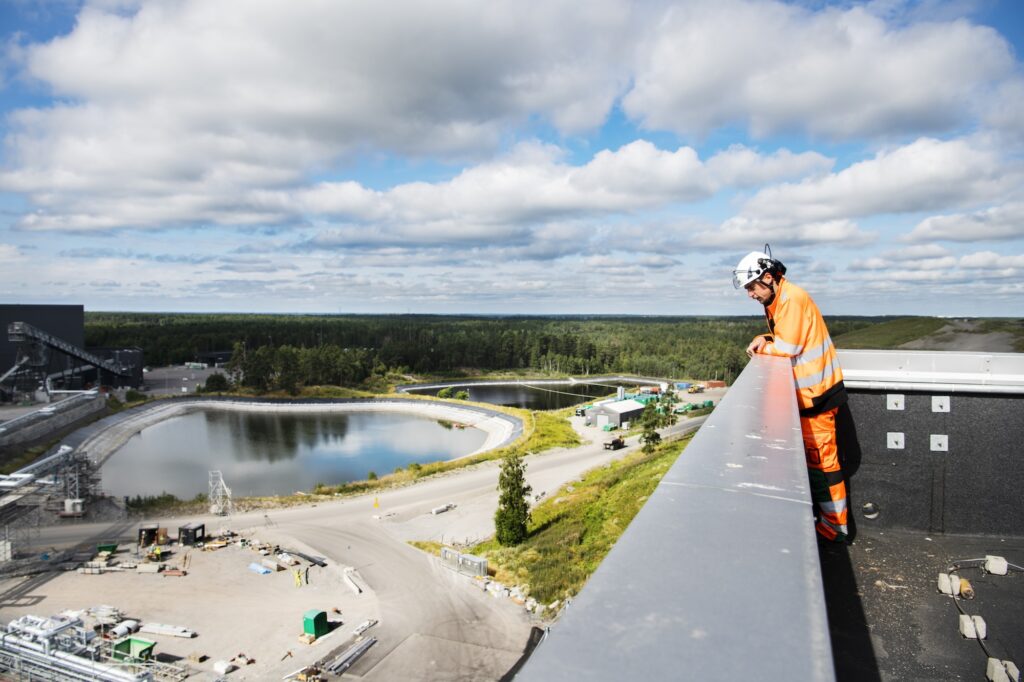